Design and sequencing of two internal climbing tower cranes, including chocking frames and associated temporary works used in the construction of One Leadenhall a 35-storey structure adjacent to Leadenhall Market in Central London.
Principal Contractor – Multiplex
Crane Supplier – Select/Multiplex Plant & Equipment
Permanent Works Designer – RBG
Fabrication & Installation – Construct-IT
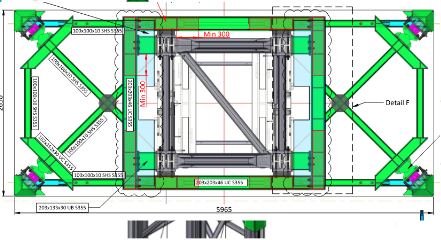
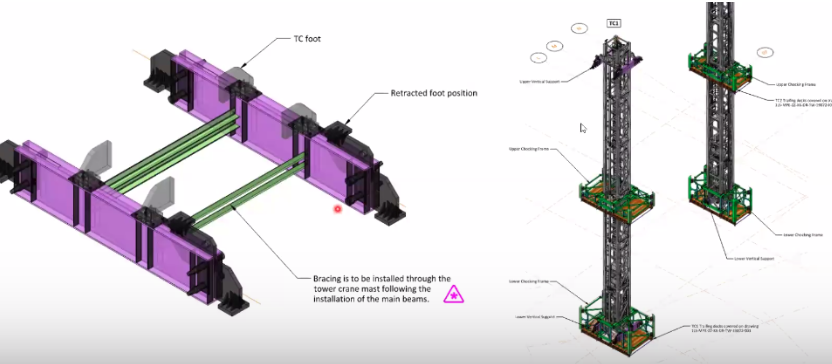
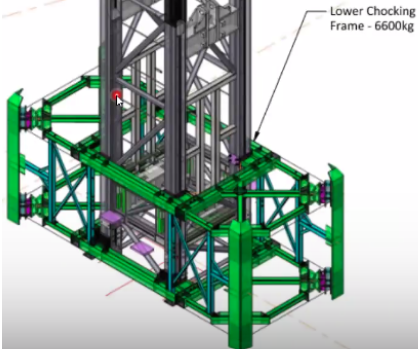
For Tower Cranes 1 and 2, the upper chocking frame was designed to be constructed at basement level, The frame was then hoisted into position, approximately 16m up the crane mast and fixed into position. The lower frame could then be constructed at basement level and fixed to the mast.
Both frames had a trailing deck to allow access during the climbing process, which was constructed at the same time as the chocking frame.
Following the construction of the frames on TC1, the vertical support beams could then be slotted through the frame and into position.
The jacking arrangement was designed using harjacks (wedge jacks) that can provide pre-load, but only has a single mechanical bolt and no hydraulics. This mitigates against the risk of failure and provides an easily inspectable jacking arrangement.
This robust system was designed to enable micro adjustments to be made during climbing with minimal intervention.
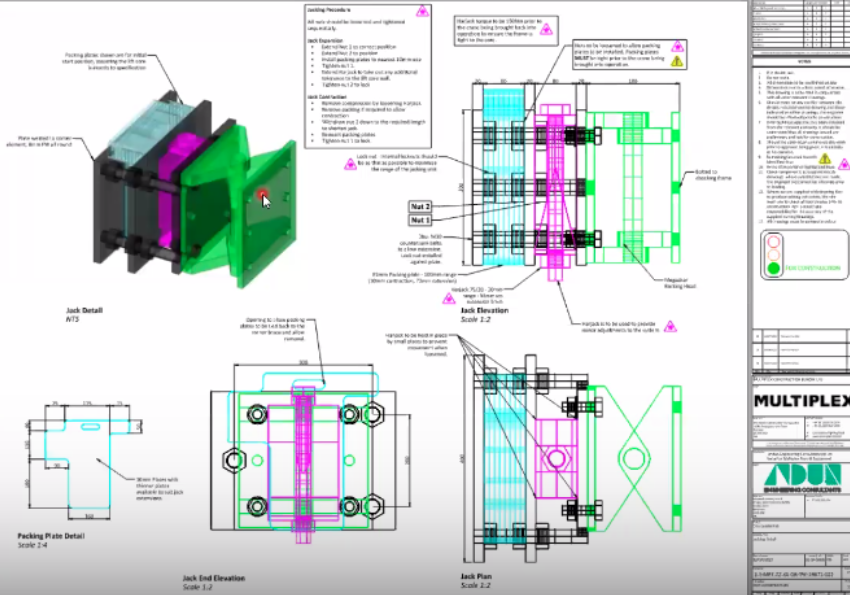