Complex demolition engineering to facilitate the removal of various obsolete heavy plant at Gladstone Docks in Liverpool.
Contractor: PP O’Connor
Client: EMR
The project included the removal of a coal stacker, a coal reclaimer and two coal unloaders within a busy operational dock. The plant that was to be demolished is pictured below.
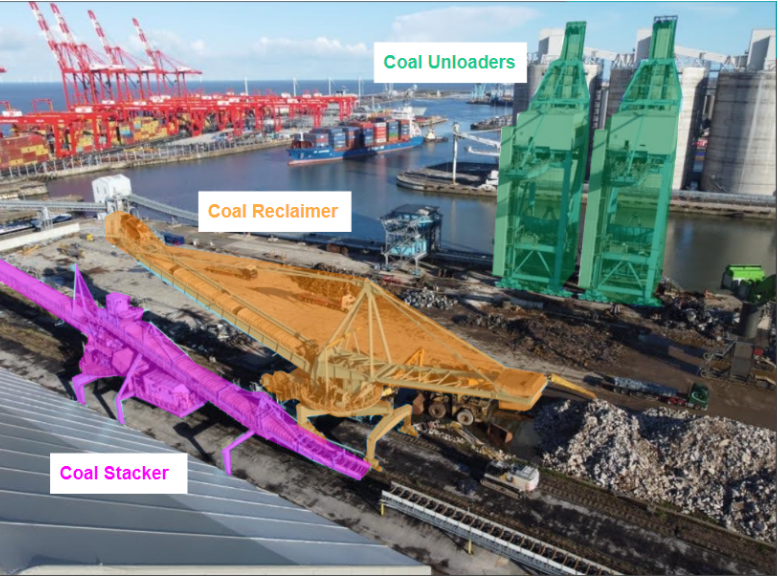
Engineering Challenges & Site Constraints
The coal reclaimer structure had a series of excavating buckets on a wheel mounted on a cantilevered arm at one end and a counterweight on an opposite arm with a pivot point in the centre.
To demolish this structure it was towed along existing rail tracks to a position away from the natural gas plant and a controlled drop of the cantilver booms was carried out. This was engineered by balancing the loads and laying loose fill beneath each drop point to absorb impact energy.
To initatel the controlled collapse mechanism, the ties were cut at the midpoint through the central block from above with the two sides of the structure then dropping away. Once on the ground then it could be processed in a safer manner from ground level with large excavators.
Whilst there maybe a high risk in dropping a structure, this risk was controlled and executed over a short period of time when a site exclusion zone is put in place.
The overall risk was lower than alternative methods that would have required extended hours of working at height or having an unstable structure in situ for an extended period.
Coal Reclaimer
The coal reclaimer structure had a series of excavating buckets on a wheel mounted on a cantilevered arm at one end and a counterweight on an opposite arm with a pivot point in the centre.
To demolish this structure, it was towed along existing rail tracks to a position away from the natural gas plant, and a controlled drop of the cantilever booms was carried out. This was engineered by balancing the loads and laying loose fill beneath each drop point to absorb impact energy.
To initiate the controlled collapse mechanism, the ties were cut at the midpoint through the central block from above, with the two sides of the structure then dropping away. Once on the ground then, it could be processed in a safer manner from ground level with large excavators.
Whilst there may be a high risk in dropping a structure, this risk was controlled and executed over a short period of time when a site exclusion zone is put in place.
The overall risk was lower than alternative methods that would have required extended hours of working at height or having an unstable structure in situ for an extended period.
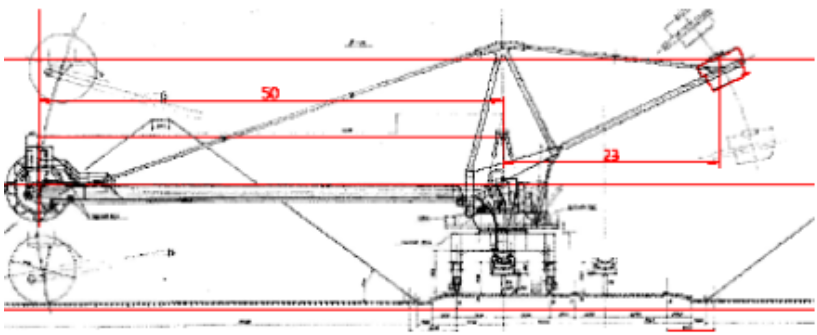
Coal Stacker
The coal stacker was demolished from one end using a large demolition spec excavator. The complexity of this process was that the boom was supported at regular points with tension ties and we were anchored in at one end.
At critical points, the ties would no longer provide support and we would have an unstable cantilever if appropriate caution, sequencing and monitoring were not applied.
Also, the plant rails ended here so we were unable to move the Coal Stacker away from the sensitive 3rd party asset on the boundary. The solution here was careful demolition removing specific elements before carrying out ‘end on’ demolition in a controlled sequence to ensure the structure maintained stability.
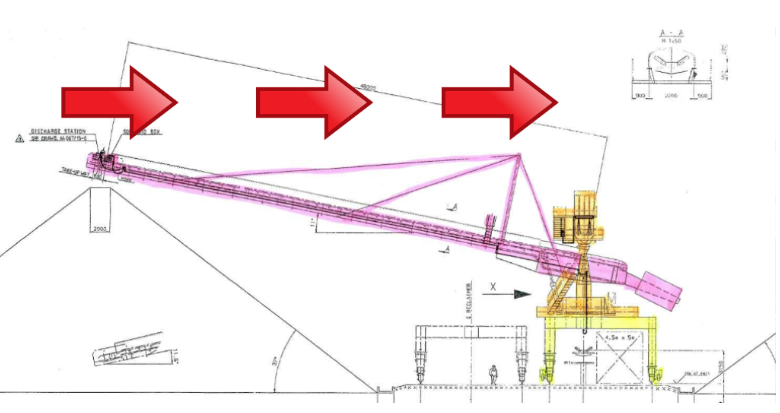
Coal Unloader
The coal unloaders were very large quay cranes directly on the edge of an operational dock. Dropping anything in the dock was to be avoided.
These cranes were not operational but were in serviceable condition structurally.
There was a wide range of information on the mechanical, electrical workings and a reasonable amount of information on the structure and geometry. But key parts of the information were missing which would enable us to make accurate weight estimates for the mobile crane.
A structural review of lifting operations including checking the integrity of lift points was carried out as well as a site measured survey, global stability review, weight take off and ongoing engineering assistance to the site team.
The structures were dismantled top down using DEMAG AC1000 which has 75te SWL @ 30m radius.
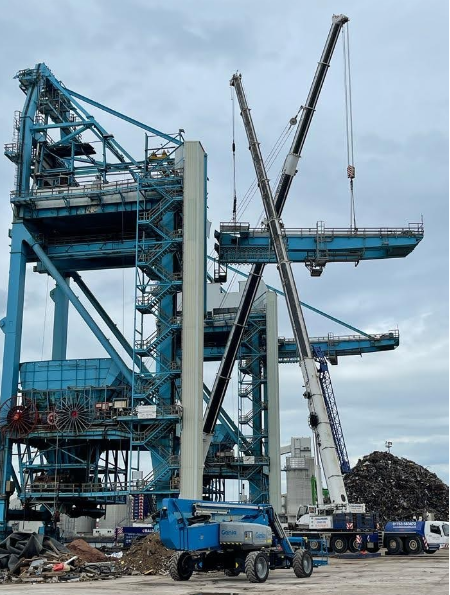